
Tesla is likely planning four versions of the 4680 battery cells
- by electrive
- Oct 07, 2024
- 0 Comments
- 0 Likes Flag 0 Of 5
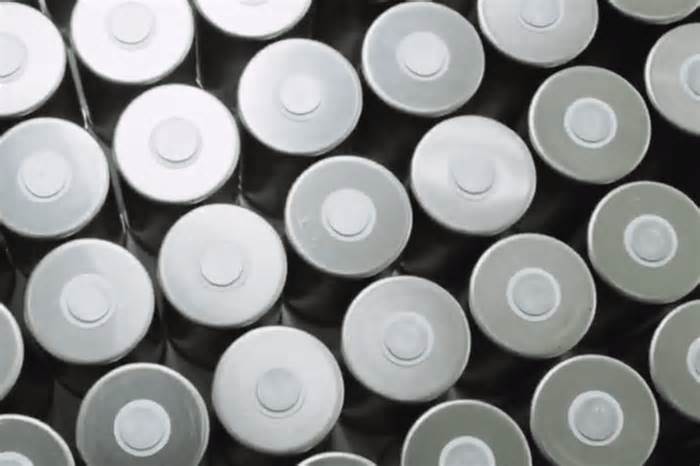
Facebook
The 4680 cylindrical cell with dry-coated electrodes was presented at Battery Day in 2020. The first Tesla production vehicles with 4680 cylindrical cells are now also available in the USA, albeit still with anodes and cathodes coated using the conventional wet process – the Cybertruck, for example, is said to have a hybrid variant with a dry-coated anode and wet-coated cathode. This summer, there were reports that Tesla intends to mass-produce the first 4680 cylindrical cells with dry-coated electrodes before the end of 2024 and use them in customer vehicles. The first cells of this type were tested in a prototype Cybertruck.
The portal The Information now claims to have learnt further details about the fully dry-coated versions of the 4680 cylindrical cells (46mm diameter, 80mm height). According to the report, four variants are planned, codenamed NC05, NC20, NC30 and NC50, each designed for different purposes.
The NC05 is described in the report as the “workhorse.” This cell variant is supposedly to be used in the upcoming Robotaxi (the presentation is scheduled for 10 October), the Cybertruck and Semi. This speaks in favour of a long service life for this cell. In comparison, the NC20 is expected to deliver more energy and, in addition to another drive variant of the Cybertruck, will also be used for an e-SUV and future Tesla models.
According to The Information, the two top versions NC30 and NC50 will have silicon components in the anode – added silicon improves the battery properties compared to pure graphite anodes. There is talk of an unspecified mixture of silicon and carbon. The NC30 is intended for the Cybertruck and a sedan, while the NC50 is intended for performance vehicles – such as the second-generation Tesla Roadster, if it comes onto the market at some point.
Up to now, battery electrodes have been coated using the so-called wet process. In this process, a powdered mixture of the active materials is mixed with solvents and other chemicals to form a paste, which is applied thinly to the carrier film. In the next step, the electrodes are dried in very large ovens, which is energy-intensive and therefore very expensive – the liquid is therefore only required for the application step. With dry coating, this is no longer necessary – and with it the need for expensive ovens. This not only reduces energy costs in battery production but also the production area required. As these work steps in battery production are not carried out in ordinary factory halls, but in special clean rooms with high-precision climate control, the costs for building and operating the clean rooms are also reduced if they can be designed to be significantly smaller (without the large ovens).
What sounds simple in theory obviously had its pitfalls during development. Back in the summer of 2024, it was stated that the cell had ‘not yet reached the level of performance and cost that Tesla had hoped for’. At the time, The Information had reported that Musk had asked the battery team to reduce costs by the end of the year and develop “one of the most important innovations” by then – likely referring to the dry coating of the cathode.
Please first to comment
Related Post
Stay Connected
Tweets by elonmuskTo get the latest tweets please make sure you are logged in on X on this browser.
Sponsored
Popular Post
Middle-Aged Dentist Bought a Tesla Cybertruck, Now He Gets All the Attention He Wanted
32 ViewsNov 23 ,2024
Tesla: Buy This Dip, Energy Growth And Margin Recovery Are Vastly Underappreciated
28 ViewsJul 29 ,2024