
Tesla Is Going To Get The Cost Of The Cybercab Down To A Staggering $15,000
- by Torque News
- Oct 29, 2024
- 0 Comments
- 0 Likes Flag 0 Of 5
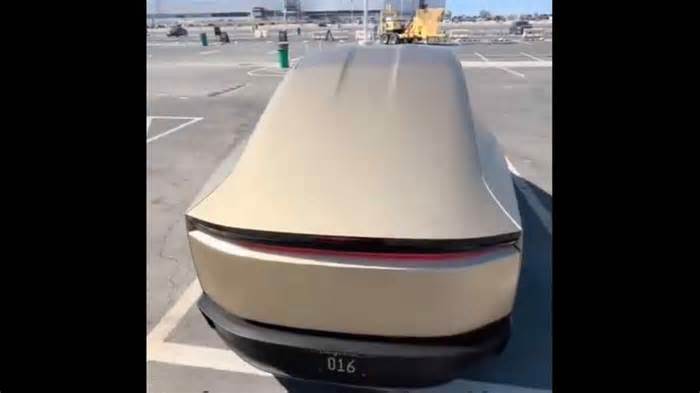
The Path to a $15,000 Cybercab Robotaxi: Tesla's Strategic Cost Reduction
Tesla is going to get the Cybercab cost down to $15,000. Here's what a breakdown of that will look like at the point mass production of millions per year is reached in 2026.
D&A expense/unit: $100 Total: $14,850
Tesla's ambition to produce a robotaxi service, potentially named "Cybercab" after the styling cues from the Cybertruck, involves significant innovation not just in autonomous driving technology but also in vehicle manufacturing.
The goal of reaching a production cost of $15,000 per unit for such a vehicle might seem ambitious, but it aligns with Tesla's history of disrupting conventional automotive economics through vertical integration, design-for-manufacture, and technological breakthroughs. Here's how Tesla might achieve this cost through various strategies illustrated in the image you've shared:
Design and Simplicity Chassis and Body Design:
Unibody Construction: Moving towards an even more integrated unibody design, Tesla could reduce the number of parts needed for assembly. The Cybercab could utilize a full-exoskeleton made from materials like 30X cold-rolled stainless steel (similar to the Cybertruck), which simplifies the body structure due to its strength and the ability to form complex shapes without multiple panels.
Reduced Complexity: By incorporating fewer components, especially in areas like the suspension and steering, Tesla can cut down on costs. For instance, using steer-by-wire instead of traditional steering systems could eliminate mechanical parts.
Interior Minimalism With Shared Mobility Focus: Since the Cybercab is designed for robotaxi services, its interior might be minimalist, removing the need for steering wheels, pedals, or traditional seating arrangements. This reduces the material and labor costs associated with upholstery, airbags tailored for human-driven vehicles, and HVAC systems.
Manufacturing Innovations and Gigacasting:
Large Single Castings: Tesla's innovation with gigacasting allows for large sections of the vehicle (like the underbody) to be cast as one piece. This not only reduces the number of parts, but also the welding and assembly time, leading to significant cost reductions.
In-House Battery Production:
Battery Cost Reduction: By producing its own batteries and advancing battery technology (like the 4680 cells), Tesla aims to slash battery costs. For a robotaxi, optimizing battery size for urban use could further reduce costs.
Increased Automation: Tesla's plan to increase the use of robotics in production lines can dramatically cut labor costs. A highly automated factory could produce vehicles with minimal human intervention, reducing not only payroll but also error rates and rework.
Mass Production:
Economies of Scale: Producing vehicles in high volumes allows Tesla to negotiate better terms with suppliers, utilize bulk purchasing for materials, and spread fixed costs over more units, significantly lowering the per-unit cost.
Vertical Integration With In-House Components: From chips to seats, Tesla's strategy of making more parts in-house reduces dependency on external suppliers, cuts down on supply chain costs, and gives Tesla control over quality and cost.
Please first to comment
Related Post
Stay Connected
Tweets by elonmuskTo get the latest tweets please make sure you are logged in on X on this browser.
Sponsored
Popular Post
Tesla: Buy This Dip, Energy Growth And Margin Recovery Are Vastly Underappreciated
28 ViewsJul 29 ,2024